Benz Thomas, Regional Head – BRCGS
Quite a few years ago, even before I stepped into the food industry, I once found a strand of hair in a cookie I was eating. My evening team time accompaniment now not only felt repulsive, but I felt cheated as well. The brand I was consuming was an MNC operating in India and this was an incident that left an indelible mark with the brand. While organisations do take a lot of steps, a lot is around the food safety culture being built in the organisation.
At BRCGS the Global Standard for Food Safety is developed by food industry experts from retailers, manufacturers and food service organisations to ensure a framework to manage product safety, integrity, legality and quality, and the operational controls for these criteria in the food and food ingredient manufacturing, processing and packing industry.
Food version 8
The current Food Standard, in its 8th edition was published in August 2018. Audits started in February and a considerable number of sites have undergone the audits. As in the earlier issues, our Food Standard has been a pioneer in introducing new concepts that enhance food safety in manufacturing sites. Two of the key new introductions in Issue 8 have been Food Safety Culture and Whistle blower policy. Both these are key towards ensuring Hygiene and thus contributing to Food Safety.
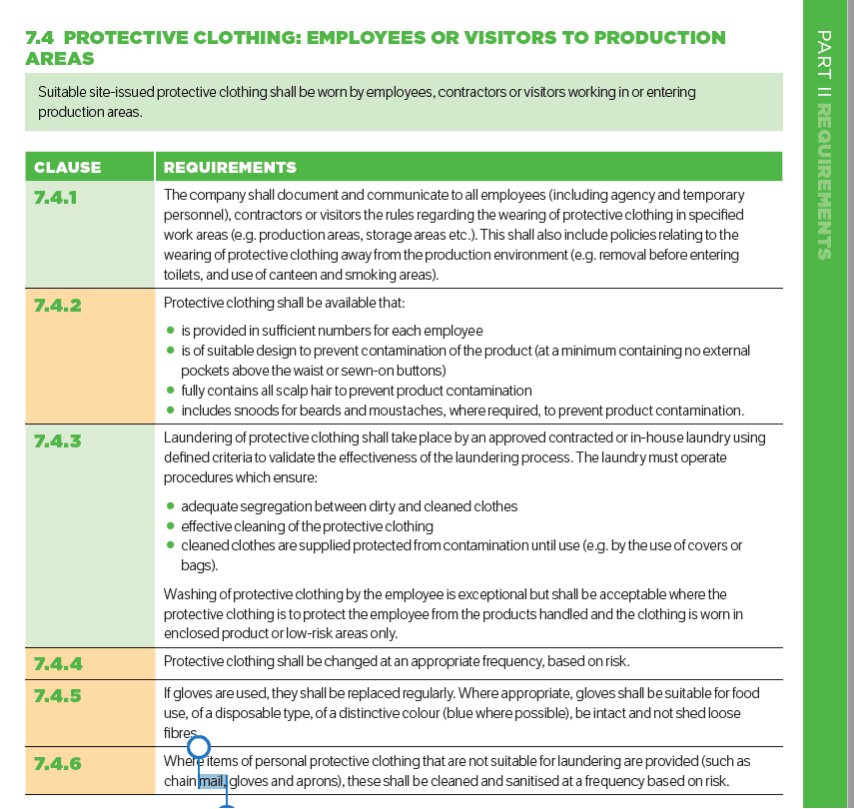
Personal Hygiene in Food Standard issue 8Section 7 of the Food Standard focuses on Personnel especially those working and visiting the manufacturing unit. The focus of this section is on Training, Personal Hygiene, Medical Screening and Protective Clothing. Subsection 7.4 particularly focuses on Protective clothing for employees or visitors to the production unit. Comprising of 6 clauses, this subsection covers the requirement of suitable protective clothing to be worn by those entering production areas. Beginning with documentation and communication the section clearly lays down the criteria for implementation. These include structure of the Protective clothing, their availability, coverage, cleaning and disposal as well as various accessories that need to be used like gloves, snoods, etc.
Insights from the Indian market
Using our insights tools, which allows us to do a deep dive into the Non-Conformance (NC) data generated from our audit reports we can get an in-depth understanding into the usage of protective clothing in the Indian food manufacturing space. For the purpose of this article, we looked at the NC data from 01 February 2019 for a 6-month period ending on 31 August 2019. This period saw India having 367 audits for the Food Standard compared to the 11000 plus audits in the rest of the world.
When the data is compared, the percentage of non-conformances being seen in the Indian sites in the section 7.4 is much higher than the global average. Non-conformances to Section 7 is four times more in the Indian audits when compared to the global numbers excluding India. In fact, clause 7.4.2 appears in the top 5 Non conformances raised by our auditors in India whereas the same clause is not there even in the top 20 globally.
A clause wise comparison tells us that Indian food manufacturing sites are much better at documentation when compared to the global ones. However actual implementation of the policies at the ground level is another issue. For clause 7.4.2 which deals with the actual protective clothing, its availability suitability and design, a lot remains to be achieved for India. It’s a similar story for clause 7.4.3 which requires cleaning and washing of protective clothing and its validation.
Protective clothing design: A lot needs to be done in India
When a qualitative search is done into the clauses, section 7.4.2 throws up a unique challenge. Most of the non-conformances cited pertain to inappropriate designing of the clothing. External pockets, buttons where they should not be present, protective clothing that does not entirely cover the workers own clothes, etc. Most of the comments were with regards to the fact that the buttons were sown on and the protective clothing wasn’t doing what they were supposed to.
Another main concern in the Indian audits happens to be the availability itself. In a lot of audits, we have seen where coats were readily available to both employees and visitors, snoods, hair nets and caps were not available. When available workers are not using them properly either due to lack of training or not having a culture of doing so. In a few cases, visitors were also seen walking around or not being provided with protective clothing in contravention to the laid-out guidelines. All this leads to chances of contamination.
Reach of scientific laundering is limited in India
In section 7.4.3, one of the key concerns raised by our auditors pertains to monitoring of the effective cleaning of the protective clothing at the time of receiving from the laundered protective clothing. Where protective clothing was commercially cleaned, a few places lacked the segregation required and clean and dirty clothing were mixed or stacked next to each other resulting in chances of cross contamination.
Commercial laundries were preferred at quite a few locations. However, most organisations did not have evidence of the efficacy of the cleaning. Our auditors have reported that there is a lack of evaluation and tests being done by the site themselves or done by the commercial laundries with results being supplied to the client for verification and record keeping. In a few cases, contracts with the laundry were found non-existent which could lead to a lot of challenges.
At a few sites it was observed that employees were encouraged to carry home the clothing and wash it themselves which raised concerns around the hygiene levels as there were no clear instructions to employees on how to wash nor was any test done to check the efficacy of the washing. In some organisations the protective clothing used in critical areas was laundered commercially whereas the rest was done by employees. A few places we did find that the process for cleaning talked about swabbing the clean clothes for microbiological testing, but in most cases, these were merely on paper with the organisations failing to produce any proof that the said process was being followed.
Protective clothing – the way ahead
The ideal situation in India with regards to Protective Clothing is still some way off. However, the path for supplying clean, hygienic and safe protective clothing is laid out clear in front of us. Be it the regulator’s focus on this or BRCGS attention to detail, the industry seems to be covering good ground. While the non-conformances seem like a challenge, however the mere fact that reporting is happening will ensure organisations take appropriate steps. Here are 5 things food manufacturing organisations should do to take care of their protective clothing.
- Design: Proper design will ensure lesser contamination chances. Seeking support from a professional organisation who understands your needs, BRCGS Standards and has experience will help overcome any challenges that may occur once you start using the piece of protective clothing on the production floor.
- Formal contracts with Scientific cleaning: Having a contractual obligation and requirements on paper is a good beginning. Manufacturing units will have to set processes in place to ensure that these contracts are followed. Also going to an organisation that scientifically cleans the clothing and keeps a check of it will help address this. Most such professional organisations will be happy to supply their efficacy data for the customer’s satisfaction.
- Employee Training: The most important cog in the whole food safety program is the employee who handles the food products. Their training and regular retraining is important as is the senior management’s commitment to keeping a check on this.
- Availability: Keeping an ample supply of the protective clothing will ensure no visitor or employee walks into the production facility without one.
- Safety culture and its measurement: This happens to be one of the critical points. While the organisation might spend a lot of money in developing the correct protective clothing, making it available, if employees do not have a food safety culture, they will not be using it thus causing contamination to the product. At BRCGS we have spent a lot of time trying to decipher this. We have come up with a Culture Excellence Module that measures 20 different aspects and puts a data against it to tell you how your investments in time, effort and money are working out.
In India there are many professional organisations that can support food manufacturers in designing and maintaining their protective clothing. These organisations use scientific cleaning methods and can provide clean clothing meeting even the stringent pharma requirements. They also offer beneficial rental services which takes away the pain and hassle of procuring, cleaning and maintaining the workwear.
There is no doubt that in India we understand the importance of Protective Clothing and its contribution to hygiene in manufacturing units. However, much needs to be done in terms of actual implementation of the processes and policies. This requires a multi-pronged approach including the set up of cleaning units that use scientific methods to clean the clothing, usage of rapid measurement kits, etc. But above all it requires the culture of food safety to be developed among each person who is related to the Food industry. Together we need to continuously work on improving the industry standards and ensuring we produce safe food.
Coming back to the incident that I began at the start of the article – Though the brand had a wide range of products that was unbeatable by competition and had a taste that I loved, it took me a long time to get their next packet into my home. It is experiences such as these, that tends to bring the focus on protective clothing inside manufacturing units and the importance of a food safety culture among employees to ensure safe food is produced each time.
If you would like to know more about BRCGS please visit www.brcgs.com
Related articles
What Should be the Ideal Recovery Path for Food Industries During COVID-19?
In the wake of COVID-19 worldwide, the food industry has been badly hit. The major disruption caused by the epidemic...
Food Safety and Hygiene: The Role of Comprehensive Audit & Testing
Access to optimal amounts of nutritious, safe, and healthy food is important for overall wellbeing. Unfortunately, an estimated 600 million,...
Providing Hygenic Food Production Clothing During the COVID-19 Pandemic
The production of food has never been more important than it is right now. With more than a quarter of...
Significance of Hygiene in the Dairy Industry : Practicing the Basic Hygiene Standards
Significance of Hygiene in the Dairy Industry : Practicing the Basic Hygiene Standards As the food production chain becomes increasingly...